
How Being Flexible Led To The Ultimate Fuel-Transfer Piping Solution
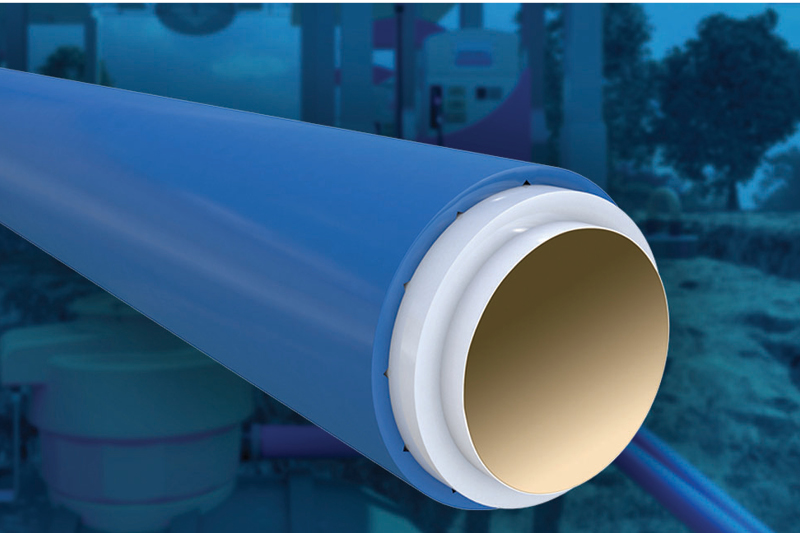
One of the definitions for the word “flexible” is “ready and able to change so as to adapt to different circumstances.”
In the early 1990s, after many decades of doing the same thing, that’s what the operators of retail-fueling sites, along with the manufacturers who created and provided the fuel-dispensing systems for those sites, were forced to be flexible – and they had to adapt quickly.
The impetus behind this need for change and flexibility was the discovery in the early 1970s that traditional underground fuel-transfer systems were prone to leaking, which was putting water supplies, the overall environment and the general public at risk. The cause of many of these leaks were the steel pipes that were commonly used to connect the system’s various underground components. This revelation essentially made the use of steel pipes in fuel-transfer systems obsolete.
As is their nature, fueling-system manufacturers showed they were indeed “flexible” by quickly coming up with a solution, and their customers were equally as quick to adopt it. By the 1980s, fiber-reinforced plastic (FRP) was being widely used in a number of industries that needed a replacement for steel. For the retail-fueling industry, FRP in the form of rigid pipe had become accepted as a legitimate replacement for steel fuel-transfer pipe, with FRP’s main advantage over steel pipe being the fact that it wouldn’t corrode and leak.
However, rigid pipe did maintain some of the shortcomings of steel pipe: it was difficult and very labor intensive to install, could only be installed in perfect weather conditions and it required glued fittings, tees and elbow joints that could be potential leak points, and if a leak were to occur, concrete would have to be broken on-site and the entire fueling system would need to be excavated in order to replace the leaking or damaged rigid pipe. This could put a strain on the fuel retailer’s bottom line from both a cost – for maintenance, repair, replacement, remediation and, in severe cases, fines or shutdown – while also creating excessive non-revenue-generating downtime for the site as the old piping was removed and the new system installed.
Creating The Ultimate Piping Solution
In no small piece of irony, the eventual answer to the fueling system’s conundrum with leaking steel pipe and the inherent operational shortcomings that carried over to rigid FRP pipe would also pay homage to the word “flexible.” In 1960, the chemical industry had invented polyvinylidene fluoride (PVDF) resin that was extremely flexible. By the 1990s, the manufacturers of retail-fueling systems had begun using piping constructed of PVDF, which gained it the name “flexible piping.” In addition to its flexibility, the PVDF-based piping was a revelation because it was an engineered plastic that also boasted low permeability, exceptional strength and durability, and resistance to aggressive fuels, chemicals, abrasion and high temperatures, all while being recyclable.
Recognizing the benefits that could have in fuel-system pipe construction, in 1996, OPW Retail Fueling, began working to develop its own flex-pipe solution. Specifically, in 1997, OPW released the industry’s newest flexible-piping system called the Primary Integrated Secondarily Contained Environmental System, or PISCES. The special sauce in the PISCES solution was a flexible primary pipe liner constructed of PVDF, along with all of the other materials in the pipe being compatible with motor fuel and bonded together during the extrusion process.
PISCES quickly became the standard in flexible piping for the industry and remained so for 10 years, or until OPW introduced its next generation of flexible piping, which it called the FlexWorks Piping System. Like PISCES was, today FlexWorks is the unquestioned standard in flexible fuel-transfer piping because – from a big-picture perspective – it provides the best possible environmental protection and economic benefits when used in fuel-transfer systems at retail-fueling sites. The proof in the pudding is the fact that FlexWorks flexible piping has been installed at more than 70,000 sites worldwide with more than 15 million feet having been sold.
In addition to its overarching environmental and economic benefits, FlexWorks piping has the following features that help make it a first-choice piping solution:
- Unmatched permeation resistance, even when used with the most aggressive fuels
- Easier and quicker installation reduces labor time and cost
- Less force required to bend the pipe
- Pipe memory has been reduced to facilitate easier connection of pipes inside sumps
- No hand-built or buried joints
- No on-site cutting, fitting, cleaning, gluing or welding of joints
- Termination points are safely located within sumps for easy access
- Can be replaced or repaired without site excavation when 4″ or 6″ access pipe is used
- Can be installed in any type of weather (a primary consideration in Canada)
- Reduced weight eases shipping and handling demands and costs
- Comes in a wide range of diameters: 3/4″, 1″, 1.5″, 2″, 3″, which makes it ideal for use in a wide range of retail setups, including high-volume convenience stores and truck stops
- Can be used in non-traditional applications, such as with fuel oil and generator supply systems
FlexWorks flexible piping has been tested under the UL/ULc-971 standard and certified for use with a complete range of motor fuels, high-blend fuels, concentrated fuels, and aviation and marine fuels, and has achieved third-party approval for use with Diesel Exhaust Fluid (DEF).
Conclusion
By acknowledging the need for flexibility when the use of steel pipes became untenable in fuel-transfer systems, the industry was able to develop the ultimate flexible solution. Flexible fuel piping has been a godsend, giving its users the highest level of peace of mind while knowing their fueling sites cannot fall prey to dangerously leaking piping. Within the flex-pipe realm, OPW has assumed a leadership position, both with its introduction of PISCES, then the development of the next-generation FlexWorks Piping System that wraps all of the standard-setting features and benefits of OPW flexible piping into one neat, reliable, durable, cost-effective and safe package.
Ed Kammerer is the director of Global Product Management for OPW, based in Cincinnati, OH, USA. He can be reached at ed.kammerer@opwglobal.com. For more information on OPW, go to opwglobal.com.