
How To Use a Holistic Approach to Upgrade an Existing Retail-Fueling Site
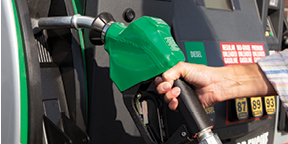
By Ed Kammerer
Welcome to Part II of our three-part series on “Holistic Fuel-Site Design.” In Part I, we focused on the importance of having all of your fuel-site components and systems working in perfect harmony, i.e., “holistically,” with any imbalances within the system being capable of adversely affecting overall performance. We noted that the first step in achieving holistic fuel-site nirvana requires casting a critical eye at the fuel-dispensing and storage systems and equipment at the site and assessing the health and performance of each component.
Because each retail-fueling site is unique in terms of specific product offerings (both on the forecourt and inside the shop), to lot and building size, to type and number of fueling components and systems deployed, it’s hard to develop a one-size-fits-all solution. So, in Part II this month, we will take an in-depth look at existing sites and the challenges their operators face in keeping a slew of individual components operating harmoniously on a daily basis. Then, we will provide some possible solutions regarding equipment upgrades that can help get all of the site’s various components and systems operating in a holistically friendly sync that will result in improved performance and peace of mind for the operator.
Bite By Bite
Perusing a list of the individual components at a retail-fueling site can bring to mind the old philosophical question: “How do you eat an elephant?” The answer: “Bite by bite.” For the retail fueler, this question becomes: “How do I take inventory of my fueling-system components?” The answer: “Piece by piece.”
For instance, just a basic list of the major individual fuel-storage and dispensing components that are used at a retail-fueling site can be daunting:
- Manhole covers
- Multiports
- Fuel nozzles
- Swivels and breakaways
- Spill containers
- Dispenser, tank and vent sumps
- Fuel-system piping
- Vent piping
- Overfill-prevention valves
- Emergency shear valves
- Vapor shear valves
- Entry fittings
- Pressure vacuum vents
- Observation monitoring wells
- A whole array of couplings
In this case, though, there are many variables to explore and record pertaining to each component. While every component may have been brand-new when the site opened, they all age at different rates. For example, a good fuel nozzle may last three to five years, but an underground storage tank can be expected to deliver 30 years of trouble-free service. The best solution to knowing at a glance the age of fueling-system components is to keep an accurate log of when they were installed, when they needed maintenance or repair, and when they needed to be replaced.
Sounds easy, but as we all know, life can come at you pretty fast sometimes, things get forgotten, misplaced or missed. This means that – short of having access to a time machine – assessing the age of specific components can oftentimes be nothing more than an educated guessing game.
However, it should be easier to ascertain the current operating condition of the components. Astute fueling-site operators will put into place a preventative-maintenance program for each piece of equipment. This program should list specific dates when each component must be inspected with any compromise of operational reliability noted, along with any necessary repairs made, and whether or not it may still be under warranty. Federal, provincial and municipal regulations and certifications also change over time, so noting whether the component is still “up to code” is also helpful when determining if it may need to be replaced.
Performing a preventative-maintenance inspection, especially with those components that are showing signs of excessive wear and tear, should also prompt the operator to consider an upgrade. The manufacturers of fueling-system components are always looking for ways to improve their current products or creating new ones. Staying abreast of the latest technological advancements in these areas can be the impetus for a component upgrade that has the capability of improving the fueling system’s performance, efficiency and operational cost.
Consider An Upgrade
On that note, OPW Retailing Fueling, Smithfield, NC, USA, is one of those companies that is always trying to expand its product offering or push the envelope in terms of what its products are able to do. With that in mind, OPW has introduced in recent years a number of innovations that have all been designed to improve the performance of critical fueling-system components. All of these can be considered when operators are looking to deploy next-generation equipment at their existing sites.
EDGE Double-Wall Spill Container: Designed in collaboration with contractors and end-users, the EDGE Double-Wall Spill Container installs in the same space as single-wall spill buckets, which saves on installation costs since it uses the old spill container’s existing infrastructure. The design features the ability to replace either the primary bucket or the secondary bucket without having to break concrete or dig up the bucket. It also offers an array of best-in-class features – vacuum test port, visual gauge, electronic-testing sensor, ribbed polyethylene skirt, removable adaptor – that significantly improves reliability, installation, testing and serviceability when compared to competitive spill containers.
71SO-T Testable Overfill-Prevention Valve: The 71SO-T is the industry’s first UST overfill-prevention valve that is testable from the forecourt surface. This means it does not need to be removed from the UST, which creates the ability to test for an overfill condition in 60 seconds per tank, not the traditional 60 minutes per UST. The design of the 71SO-T also allows for easy installation with no need to break concrete or use special manholes.
10 Plus Series Emergency Shut-Off Valves: The 10 Plus is the retail-fueling industry’s only emergency shut-off valve that is designed to protect against the potential hazards of undetected shear groove leaks in the dispenser piping that are caused by anything from low-impact incidents to full-blown dislodged or pulled-over dispensers. The unit’s patented SmartGuard design contains shear groove leaks to prevent fuel from leaking into sumps, which helps reduce the risk of fire, explosion, personal injury, property damage, environmental contamination, product loss and costly cleanup at the fueling site.
TSE Tank, DSE Dispenser & VSE Vent Sumps: These three sump styles comprise the members of OPW’s E-Series Sump family. All are constructed via the innovative Sheet-Molded Compound (SMC) manufacturing process that ensures a finished product with consistently thick and smooth inner and outer walls, which makes it easier to install entry fittings and ensure that they are leak-free. The expedited construction process for all three models also helps ensure that demanding delivery lead times are met for every customer.
Pre-Plumbed DSE Dispenser Sump: Using the same Advanced Composite Technology manufacturing process as the DSE sump, the Pre-Plumbed DSE Dispenser Sump is shipped to the fueling site with factory-assembled and tested components. This makes the Pre-Plumbed DSE Dispenser Sump an ideal solution for fuel-site operators who wish to simplify their installation while saving time and costs.
Rigid (REF) and Hybrid (HEF) Entry Fittings: The REF features minimal exposed rubber but is still able to accommodate ground movement and provide sealing redundancy for maximum product contamination and protection against water intrusion. The HEF combines the best features of the REF (a hard-shell exterior resistant to ground movement) and the Double Entry Boot fitting (an easily accessible flexible inner half) to offer maximum product containment and water-intrusion prevention with easy piping installation
14C/14HC Diesel-Capture Nozzles: Members of OPW’s 14 Series family of clean-fueling nozzles, these models have been designed to minimize the potential for diesel dripping down the spout after fueling via the diesel-capture chamber, which helps keep fuel off drivers’ hands and clothing, the dispensing equipment and the ground, creating an overall cleaner and more appealing fueling experience. The 14HC nozzle brings those benefits to high-flow diesel-fueling activities, particularly those that are common at truck stops and high-volume c-store sites that feature truck-fueling islands.
XC Extreme-Cold Nozzles: Perfect for use in cold Canadian winters, OPW’s 11A and 11B nozzles for automobile fueling and 7H and 7HB automatic shut-off nozzles for high-flow truck, bus and heavy-duty equipment fueling have been upgraded for use in temperatures as low as -54ºC (-65ºF).
Fibrelite Watertight Composite Manholes: These are the industry’s leading watertight, easy to remove, non-bolted composite manhole covers. Available in a large selection of shapes, sizes and colors, they provide quick access to multiport and single-port fill sumps, interstitial sumps and monitoring wells.
Island Forms: Available in standard straight, hourglass and build-your-own designs, OPW island forms facilitate the construction of concrete forms that are used to protect fuel dispensers and streamline traffic patterns
Conclusion
Fuel-site operators who take a committed approach to accurately and reliably assessing and recording the condition of the many components that make up their fuel-storage and dispensing system will be ahead of the game when it comes time to repair or replace aging equipment. Those that take the next step and use equipment repair and replacement activities to upgrade to enhanced or new components will find themselves even further ahead in the game. To that end, OPW Retail Fueling offers a wide array of innovative solutions, many of which are upgraded versions of components that have already proven their worth and capabilities over many decades of successful fueling-site deployment and operation.
Ed Kammerer is the senior director, global product management for OPW, based in Cincinnati, OH, USA. He can be reached at ed.kammerer@opwglobal.com. For more information on OPW, go to opwglobal.com.